There’s a persistent school of thought that safety is an extra layer imposed on top of work, so minimizing this layer would mean more work gets done in the same amount of time. It’s hard to argue with this logic unless you understand what safe work practices entail.
Those practices, when fully understood, consistently and correctly implemented, and integrated into the normal workflow and procedures, increase not only safety but also efficiency and work quality. How can this be? If you skip steps instead of performing them, don’t you save time?
Consider a simple task such as cutting wood. Let’s say you need to cut a sheet of plywood into two 4-ft squares, so you can use one square to mount some boxes and control switches.
What’s demonstrated by cutting the plywood the correct way is a concept called working methodically. If you’re not methodical, how might you cut it?
For example, maybe Jason lays the plywood on a couple of sawhorses and has Joe, his helper, hold it steady while he cuts off half with his circular saw. That seems like it’s a lot faster than the way Robert does it.
Robert clamps the piece to a contractor-grade fold-up worktable and supports the “waste” part on a couple of sawhorses. He uses a contractor-grade saw guide to make a perfect cut. It may appear he was fussy and wasted quite a bit of time.
But unlike Jason, Robert did not need to:
- Tie up a helper.
- Go back over that wandering cut to try to clean it up.
- Fix the wood splinter problem at the end of the cut.
- Damage both halves of the plywood sheet.
- Risk getting hurt by the kickback caused by binding on the blade.
- Figure out how to hide the bad edge when mounting the plywood.
Do you see from this simple example that Jason took more time to do worse work while at greater risk of injury to himself and one other person? Do you also see that by working methodically, Robert reduced the helper’s risk to zero because no helper was needed?
Job planning is safety planning
The first step in working methodically is to develop the methodology. This is another way of saying you plan the job and each task comprising it. You can use job safety planning to do this.
In NFPA 70E, Standard for Electrical Safety in the Workplace, we find three requirements for job safety planning [Sec. 110.3(I)(1)]. This plan must:
- Be completed by a qualified person.
- Be documented.
- Include information such as a description of the job, individual tasks, and work procedures.
You could remove the word “safety” from this, and it would apply to every job that you want to do efficiently and correctly. Requirement No. 3 for the plan also includes identification of the electrical risks, an electric shock assessment, and an arc flash assessment. But aside from those safety specifics, job planning is safety planning and vice versa. A job that is not properly planned cannot be properly performed, which means it will be performed inefficiently. And because job planning is safety planning and vice-versa, job safety planning is essential to performing a job efficiently.
Job briefing
One way to save time is to skip the job briefing [Sec. 110.3(I)(2)]. This is, after all, another one of those pesky safety requirements. It can take the crew leader 20 minutes to put together the information and contact the concerned parties. If it’s a crew of four attending a 15-minute job briefing, that’s a man-hour of labor plus another 15-minute delay in getting started. One eager crew leader at an Alabama manufacturing plant did the math and decided to save his company some money by skipping this step. If anybody had questions, they could just ask him. The problem is that people often don’t know that questions need to be asked.
The equipment in question had to be run until a particular order was completed and shipped out that day. A key customer was counting on that order. So production agreed to let lockout/tagout occur at 14:15. The operators would start an orderly shutdown at 14:00, which was about the time the last piece from that line would complete the outgoing shipment.
Production stipulated that, because this machine produced $325,000 of revenue per hour, they wanted the lockout/tagout walked down no later than 13:30 so it would be done without a hitch once production released the equipment for downtime. The superintendent said not to do anything until production confirmed the critical run was complete. In an NFPA 70E-compliant job, all of this would have been known to the whole crew. But this was not an NFPA 70E-compliant job.
Because there was no job briefing, the walk down got confused with the lockout, and power to the equipment was interrupted prematurely. But the equipment could not be restarted as if nothing had happened for two reasons. First, the start-up process took almost 10 minutes. Second, the interruption happened at the worst possible time during machine operation, causing the work in process to damage the machine. The damage would take several hours to repair.
A safety incident did not result from this, but it could have. However, this attempt at cost savings cost the company $1,460,000 in lost revenue, plus $7,500 in repair costs, plus the labor costs of idled production workers. Then there’s the business cost to the customer, who was counting on that shipment. The economics of skipping the job briefing just were not there. They never are.
Methodical performance
The onus of getting the planning and communication right falls primarily on the crew leader. What about the rest of the crew? Does it matter how they carry out the plan? Yes. For efficiency, safety, and quality, they must perform methodically.
Methodical performance by each crew member is task-specific. Each person must determine and follow the right steps in the right sequence. In the plywood cutting example, how did Robert know to take all of those steps? And why didn’t Jason know? Or if Jason knew, why didn’t he take them?
The answers involve the concept of craft capability applied with an attitude of professionalism. Meeting the NEC’s workmanship requirement of installing equipment in “a professional and skilled manner” [Sec. 110.12] has been a subject of discussion for decades. Nobody’s really pinned it down with a prescriptive text. That’s probably because while the skills can be added to a person’s repertoire, professionalism must be one of that person’s personal principles.
Any of us can see the difference once the work has been done. The professionally mounted raceway has the support brackets at precisely measured intervals, and the unprofessionally mounted raceway has them at “eyeballed” (random) intervals. The latter just doesn’t look right, and it’s not as strong as the former.
Professional results come from working methodically and executing specific steps to achieve specific goals within the task at hand. The methodical electrician has a rhythm going, doesn’t have to rethink things at every step, and doesn’t have to waste time redoing work. In that plywood cutting example, Robert didn’t need to constantly adjust his saw or spend time trying to fix a bad cut. Nor did he have to worry about kicking the board into his absent helper’s gut or kicking the saw back over the fingers of his left hand. These kinds of things often happen to people like Jason and his helper.
The idea of working methodically permeates NFPA 70E. Get the right steps worked out and then follow them. Safety isn’t added onto the job — it’s integrated into it.
To perform tasks methodically:
- Identify the correct method. If you are a qualified person, you should know what this is. Use that method every time. Hint: If it smells like a shortcut, it’s not the correct method. The correct method is geared toward getting things right the first time — not cutting corners.
- Identify and use the tools needed to execute the correct method (just as Robert did).
- Do a quick mental walkthrough (visualization) of performing the work. As you visualize, move your hands as if you are using tools (if that helps). Getting an “oops” moment here (e.g., “I’d better put an insulating blanket over that”) is a potential lifesaver. Or an “oops” moment could mean you’re going to need a specific driver bit halfway into this, so now is the time to add it to your tool list rather than try to “make do” and injure yourself or mess up the work later.
- Execute the correct method by calmly and carefully performing each required step in the correct sequence.
Pressure relief
Time pressure is the most common reason people forego working methodically. They mistakenly believe they will get it done faster by being less rigid. Counter any time pressure by reciting such adages as “never enough time to do it right, always enough time to do it over” and “measure twice, cut once.”
About the Author
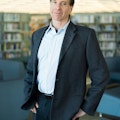
Mark Lamendola
Mark is an expert in maintenance management, having racked up an impressive track record during his time working in the field. He also has extensive knowledge of, and practical expertise with, the National Electrical Code (NEC). Through his consulting business, he provides articles and training materials on electrical topics, specializing in making difficult subjects easy to understand and focusing on the practical aspects of electrical work.
Prior to starting his own business, Mark served as the Technical Editor on EC&M for six years, worked three years in nuclear maintenance, six years as a contract project engineer/project manager, three years as a systems engineer, and three years in plant maintenance management.
Mark earned an AAS degree from Rock Valley College, a BSEET from Columbia Pacific University, and an MBA from Lake Erie College. He’s also completed several related certifications over the years and even was formerly licensed as a Master Electrician. He is a Senior Member of the IEEE and past Chairman of the Kansas City Chapters of both the IEEE and the IEEE Computer Society. Mark also served as the program director for, a board member of, and webmaster of, the Midwest Chapter of the 7x24 Exchange. He has also held memberships with the following organizations: NETA, NFPA, International Association of Webmasters, and Institute of Certified Professional Managers.