A Data-Informed Approach to Preventing Electrical Incidents
Electricity continues to be a leading cause of electrical injuries and fatalities in the workplace according to data recently compiled by the Electrical Safety Foundation International (ESFI). As a workplace hazard, electricity is unique; it is nearly ubiquitous across all workplaces yet undetectable by sight and smell. These factors and others have prompted the Occupational Safety and Health Administration (OSHA) to declare electricity one of their “fatal four” construction hazards. With only modest improvements in worker electrical fatality rates year over year, more can be done to educate workers and job-site managers about the importance of electrical safety. This article outlines three areas of emphasis using a data-informed approach that can assist employers as they seek to create safer workplaces.
Getting employers to buy in to safety initiatives
According to a 2024 survey conducted by ESFI and Wesco, nearly a quarter of safety professionals said that “cultural adoption” of safety protocols is a challenge to overcome. Convincing workers and executives to buy in to a culture of safety can be difficult, but there are several strategies that company decision-makers can employ to get employees at all levels on board:
- Empower workers to speak up when they feel uncomfortable. While workers should be properly trained and equipped for every job, unexpected conditions can arise at any time. Workers should know when to say when and stop work if they do not have the training or protection required for a task. Workplaces should instill a culture that allows workers to speak up about concerns without consequences.
- Learn to speak the language of the audience. When discussing safety measures with individuals at the management and executive level, for example, emphasis can be placed on cost savings and return on investment. Workplace accident claims are costly – averaging about $40,000 per claim according to the National Council on Compensation Insurance — and companies can incur steep fines for failing to address workplace hazards. Each OSHA violation carries a penalty of up to $16,550 in 2025, and repeated or willful violations of OSHA standards can land companies a $165,514 fine. Additionally, downtime due to surges and failing to perform preventative maintenance can be costly to both workers and equipment. The median time away from work for electrical incidents between 2021 and 2022 was five days, and equipment failure can cost facilities thousands or even millions of dollars per hour.
- Take worker feedback seriously. If a workplace is having a hard time getting workers to buy in to a safety protocol — whether that is using personal protective equipment properly or adhering to lockout/tagout procedures — it is important to find out why. Is their equipment fitting properly? Do they have privacy concerns about connected safety monitoring devices? Enabling a workplace culture where workers feel comfortable offering feedback can help alert decision-makers in the company to potential issues before something goes wrong.
- Award early adopters. Companies can also try to incentivize the usage of safety equipment by awarding early adopters of safety equipment or protocols. Incentives could include financial bonuses, recognition, and increased opportunities to lead others during certain activities.
Tackling power line-related workplace injuries and fatalities
Narrowing in from cultural adoption of safety more broadly, addressing specific electrical hazards in the workplace is imperative. In the available data on workplace electrical hazards, one issue continues to come up year after year as a leading hazard to workers. From 2011 to 2023, overhead power line contact accounted for 48% of workplace electrical fatalities. Among these, 87% occurred in non-electrical occupations. Taken together, these two data points underscore the need for robust training and site-specific safety measures.
The first barrier to workplace injury is knowledge — and proper training for a job is key. This is especially true when a job involves electrical risks that cannot be eliminated or substituted, like working on a residential property that is close to a power line. Electrical safety training cannot be overlooked simply because a job does not directly involve electrical work. Each year, construction workers, tree trimmers, truck drivers, painters, and others lose their lives due to contact with power lines. When developing training for workers, employers should be conscious of both direct and inadvertent risks of the job and clearly express the stakes of failing to follow safety procedures.
Additionally, site-specific safety plans are a critically important step in the development of any work plan involving electrical risks. While the process of, for example, painting the exterior of a house is similar from job to job, the conditions of each job site can vary significantly. Each job site should be inspected before work is performed on it to develop a site-specific safety plan, and these plans should be reevaluated if conditions change or if new hazards are discovered in the course of work.
Emerging safety technologies
In recent years, several safety technologies have been introduced to the market that help to mitigate or eliminate electrical injury risk. Often referred to as connected safety devices, this equipment integrates digital technologies into the workplace. Examples of connected safety devices include wearable devices that provide haptic feedback in response to unsafe movements, continuous monitoring video devices that use artificial intelligence to analyze conditions in real time, and environmental sensors that check for hazards like floor moisture or water leaks. These devices are crucial for worker safety, as a significant portion of electrical injuries and fatalities in the workplace occur due to employees working directly on or near energized parts. Devices that monitor or protect equipment, such as surge protective devices, also help to keep both workers and machinery safe and save organizations money. Automating some monitoring tasks can also reduce the need for manual inspections that expose workers to energized equipment.
Despite the life- and cost-saving potential afforded by emerging safety technologies, they are not always well received by workers and executives. For the former group, these new devices can be seen as intrusive. Because these technologies tend to rely on continuous observation or artificial intelligence, they can sometimes make workers feel like they are being monitored. It should be noted that continuous monitoring technology can (beyond providing protection against hazards) also provide protection to workers against liability in situations where there is a question as to whether procedure was followed. Executives, on the other hand, may balk at the cost of implementing new safety technologies, especially given the fact that there is often no immediate and measurable return on investment as a result of implementing new safety devices. The consequences, however, of ignoring these emerging technologies can be fatal.
Conclusion
Proactively preventing workplace electrical incidents not only saves lives but also conserves time and resources. While some organizations may have difficulty with the costs of instilling a culture of safety through training and new technology, the livelihoods of workers must always be a primary concern compared to the cost burden. Beyond this, enhancing safety in the workplace can help organizations avoid penalties, downtime, and lost productivity due to injury or death. Additionally, vendors who produce and sell connected safety devices are beginning to offer solutions for a wider variety of workplaces, meaning that even small organizations can take advantage of these emerging technologies.
Even with enhanced safety measures like connected safety devices, knowledge is the most important tool that a worker can bring to the job site. Proper training remains the foundational element to a safe workplace, and frequent evaluation and reevaluation of site premises is essential regardless of what other protections are utilized. Without a strong current of safety running through the circuitry of an organization, these important steps can be overlooked in the name of expediency or efficiency. It is crucial for employees at all levels of an organization to buy in to a culture of safety and establish that safety is in the best interests of everyone — from the factory worker to the CEO.
About the Author
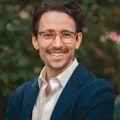
Evan Jones
Evan Jones is the Communications Representative for the Electrical Safety Foundation. He has several years of experience in communications roles in nonprofit and academic settings.
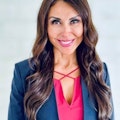
Lorenza Ordonez
Lorenza Ordonez serves as the Global Director of Safety Sales and Strategy for Wesco. Within this role, she is the leader of Connected Safety. She is responsible for empowering our global safety organization to deliver comprehensive safety solutions and services to our customers. Ordonez brings decades of expertise in safety, strategic market analysis, and sales management to Wesco.