While walking through a plant in southeast Missouri, an electrical consultant noticed an employee standing on the top rung of a ladder. The consultant was escorted by an engineer who was employed by the plant. The consultant told his escort about the problem, and his escort immediately went to the ladder and asked the person on it to come down so they could talk. They spent a few minutes talking about the unsafe act.
While walking through a plant in northeast Mississippi, this same consultant noticed several panels with unused openings that were not covered or filled. As in the Missouri plant, the consultant was escorted by an engineer who was employed by the plant. But he did not say anything. Why the difference? One thing he noticed upon entering the plant was nobody was wearing safety glasses. That included his escort, who gave the consultant a puzzled look when the consultant stopped at the door to put on his own safety glasses. Another was that people were wearing sneakers. A third was that (even though the plant was full of rotating equipment), many operators were wearing long-sleeved shirts.
As tough as it might seem to remain silent when you are safety-oriented, you aren’t there to teach your client safety. The disregard for it at the second plant meant a safety message of any sort would not be heard, much less received and acted upon. In the first plant, one person got a little careless and the message was heard, received, and immediately acted upon.
So always take the lay of the land before offering safety commentary or advice — except where your own safety (or that of your crew) is at risk. Then the lay of the land will tell you whether you can expect resources and support from the client. In a safety-conscious facility, all you have to do about unsafe conditions is report them. You won’t have to wait long for resolution or further instructions. In a facility that is not safety conscious, you’ll have to protect yourself (and crew) using the appropriate means, regardless of the client’s support or lack thereof — but it’s often smarter to just refuse to work there.
In many cases, there’s an easy solution. Barricade the area with red tape, and fix the unsafe conditions. This has its limitations, however. For example, if half the cover bolts are missing on switchgear doors or panel covers, are you going to spend time and money replacing them? And since that defect shows this equipment has not been properly maintained, simply replacing the missing bolts doesn’t address the unknown (as of this point) condition of the equipment or the resulting safety issues. The barricade method is suitable for things like allowing you to move flammables away from the area, keeping curious operators from walking through the area, and preventing lift trucks from driving through where you’re working. It does not solve equipment-related unsafe conditions.
For the tougher issues, such as unknown equipment condition or egregious NEC violations, you need a different approach — and your project manager isn’t going to like having to deal with it.
If equipment has not been maintained per the applicable industry standards, it is in an unknown condition. This means you cannot apply NFPA 70E Art. 130. You cannot do things like perform an infrared scan or assess the power quality with a portable power analyzer. You must assume that equipment, while energized, could blow up at any second with no warning. To do any work on it, or even to begin a basic assessment, you must establish an electrically safe work condition per Art. 120. Clients generally don’t like having their equipment shut down, and this issue is what your project manager is not going to like dealing with.
There’s always a risk the client will refuse a shutdown, saying you can do the work without it or they’ll get somebody else. That risk is worth taking. And not just for safety, clients who cheat their own employees this way also cheat their contractors. If you walk away from this client, you will also be walking away from scope creep, nuisance callbacks, and other costs that can suck away any profit your firm might have made. Your project manager should know to document the problems, get internal approval at your firm, and then issue a written technical warning to the client. If the situation is bad enough, that document will need to be sent to the serving utility or other AHJ; as to how bad, that is a call your firm’s senior management will have to make.
Another risk is that your company may be named in a civil suit due to an explosion that happened months after you left, because being the electrical experts you were negligent when you let this hazard slide. Just defending against that is expensive, but your firm can eliminate that risk with a proper paper trail and proper notifications to the proper authorities.
An electrical services firm in southern Illinois pushed the shutdown refusal issue by saying they were ethically bound to contact the serving utility. In this case, the EGC measured 277V to ground and there were feeders consisting of parallel conductors of different sizes (in each pair, the smaller conductor had obvious insulation damage from the heat). The utility’s crew leader took one look at those feeders and said the plant would be shut down. The contractor may have saved the lives of the employees at the plant that day, but the client was not happy with the contractor. However, those hazards got addressed so there was no ticking time bomb of civil liability, and the contractor went on to other clients whose facilities were safe to work in.
About the Author
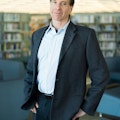
Mark Lamendola
Mark is an expert in maintenance management, having racked up an impressive track record during his time working in the field. He also has extensive knowledge of, and practical expertise with, the National Electrical Code (NEC). Through his consulting business, he provides articles and training materials on electrical topics, specializing in making difficult subjects easy to understand and focusing on the practical aspects of electrical work.
Prior to starting his own business, Mark served as the Technical Editor on EC&M for six years, worked three years in nuclear maintenance, six years as a contract project engineer/project manager, three years as a systems engineer, and three years in plant maintenance management.
Mark earned an AAS degree from Rock Valley College, a BSEET from Columbia Pacific University, and an MBA from Lake Erie College. He’s also completed several related certifications over the years and even was formerly licensed as a Master Electrician. He is a Senior Member of the IEEE and past Chairman of the Kansas City Chapters of both the IEEE and the IEEE Computer Society. Mark also served as the program director for, a board member of, and webmaster of, the Midwest Chapter of the 7x24 Exchange. He has also held memberships with the following organizations: NETA, NFPA, International Association of Webmasters, and Institute of Certified Professional Managers.