OSHA provides the requirements for the Hazard Communication Standard (HCS) in 29 CFR 1910.1200. The purpose of the HCS is to ensure that employees understand health and safety information concerning the hazardous chemicals they are likely to encounter on a given job site.
It might seem like the details are where employers stumble and get cited. The reason employers stumble on the details is they don’t understand the major things that OSHA wants them to do. Blindly wading through the details without understanding how they relate to the whole will make compliance difficult. But if you step back and gain an understanding of the basics, those details tend to fall into place.
HCS is different from the other OSHA standards, which are prescriptive action standards. A prescriptive action standard provides specific actions you must take or it provides specifics about an action you take. For example, Subpart K (electrical) requires that a conductor used as a grounded conductor shall be identifiable and distinguishable from all other conductors [1926.404(a)(1)].
The HCS standard, by contrast, is all about communicating chemical hazard information to the employees. The first thing to understand is that HCS is a communication standard. So with every effort made to implement HCS, ask yourself, “What needs to be communicated here, and how clear can I make it?”
The communication is done primarily through container labels and the material data sheet (MDS) for each hazardous chemical. Among other responsibilities, employers need to ensure the containers have labels and the MDS is available.
One of those other responsibilities that employers have is to develop, implement, and maintain, at each workplace, a written hazard communication program. This program has to meet the specific requirements spelled out in 1910.1200(e). The employer must provide a copy of this to any employee who asks for it.
Another responsibility that employers have is to train employees on the hazardous chemicals in their work area and on the relevant data sheets. OSHA specifically mentions this training must be effective. The training has to cover specific things, including both the dangers presented and the measures employees can take to protect themselves (including specific procedures the employer has implemented for such protection).
Some tips for employees:
- Ask for a copy of your facility’s HCS. Take the time to read it. Jot down any questions that come to mind, and ask the safety director or similarly responsible person to answer them.
- Get the MDS for any chemical you are using for the first time. The MDS follows a standard format, you can easily zero in on what you need to know. Three vital things to know are ventilation requirements, PPE requirements, and medical attention requirements. If you do not know these things, do not use the chemical.
- Find out if there’s any notification system for when an MDS changes. If not, you’ll need to check the MDS each time you access a new batch of whatever chemical that is.
- Don’t substitute PPE. For example, if the MDS requires a charcoal canister mask, don’t use a dust mask instead. If you do not have the correct PPE, do not use that chemical. Report the problem to your supervisor.
About the Author
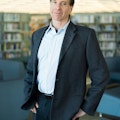
Mark Lamendola
Mark is an expert in maintenance management, having racked up an impressive track record during his time working in the field. He also has extensive knowledge of, and practical expertise with, the National Electrical Code (NEC). Through his consulting business, he provides articles and training materials on electrical topics, specializing in making difficult subjects easy to understand and focusing on the practical aspects of electrical work.
Prior to starting his own business, Mark served as the Technical Editor on EC&M for six years, worked three years in nuclear maintenance, six years as a contract project engineer/project manager, three years as a systems engineer, and three years in plant maintenance management.
Mark earned an AAS degree from Rock Valley College, a BSEET from Columbia Pacific University, and an MBA from Lake Erie College. He’s also completed several related certifications over the years and even was formerly licensed as a Master Electrician. He is a Senior Member of the IEEE and past Chairman of the Kansas City Chapters of both the IEEE and the IEEE Computer Society. Mark also served as the program director for, a board member of, and webmaster of, the Midwest Chapter of the 7x24 Exchange. He has also held memberships with the following organizations: NETA, NFPA, International Association of Webmasters, and Institute of Certified Professional Managers.