In your workplace, you probably use many different chemicals in the form of solvents, paints, varnishes, and lubricants. The workplace itself contains additional chemicals, including those used by other trades and those used in production processes. To help you protect yourself from chemical hazards, OSHA created the Hazard Communication Standard (HCS) in 1989. It has three main missions:
1. Set standards for manufacturers of hazardous chemicals.
2. Set standards for employers of people working with hazardous chemicals.
3. Ensure hazard information is available to people working with hazardous chemicals.
Because it gives you the right to know the hazards of the chemicals you work with or around, HCS is a “Right-to-Know” (RTK) law. States have additional RTK laws. But unless your state has an OSHA-approved “state plan,” HCS replaces state laws.
Your company may have different RTK policies at different facilities because it must comply with the (OSHA-approved) laws in the state where that facility is located. If you’re a contractor traveling from state to state, the policy on one job may differ from the policy on the previous job.
HCS primarily uses five tools:
1. Hazard evaluation.
2. Warning labels.
3. Material data sheets (MDS).
4. Employee training.
5. Written program.
Hazard Evaluation
The manufacturer performs a hazard evaluation on a given chemical, usually making use of product safety studies. Then, the manufacturer provides the safety information that you find on product containers and in the MDS. Note: MDS were formerly known as material safety data sheets (MSDS), but the terminology and HCS itself have been “harmonized” to European standards (see Harmonization Sidebar below).
Obviously, manufacturers can’t know what hazards you face in your work or how to deal with them. Your employer must ascertain those things and then share that information with you. The sharing is done through methods such as training, procedures, safety meetings, supervision, and signs. Then, there are your responsibilities. The manufacturer evaluates the chemical hazards, and the employer evaluates the workplace hazards. But you must evaluate both —sometimes that means not doing the job until a safety issue is resolved.
Regardless of what the manufacturer does or what your employer does, you are the only person who can make you safe. That is your primary job from the moment you come on-site. You’re expected to read the product labels. You’re expected to read the MDS. You’re expected to contact your supervisor if information is missing or unclear. And, if you have a family, they are expecting you to come home after work. That’s a lot of expectations. You can decide to live up to those expectations and work safely, or you can let a lot of people down. It’s not a hard choice to make.
Warning Labels
We see warning labels so much, most of us must consciously work to avoid ignoring them. That effort is worthwhile, especially when working with hazardous chemicals. Those labels aren’t there to protect the manufacturer from liability (though they help do that). A manufacturer’s legal counsel is concerned with whether the company avoids fines and civil liabilities, but OSHA isn’t. OSHA is concerned about the safety of the employee, and thus those mandated labels are there to help you protect yourself.
Labels include body-part specific information. A label may have one warning about your eyes and another about your skin.
Use the label information in your job planning. For example, what ventilation and personal protective equipment (PPE) will you need? What if it gets on your skin? The labels are usually in tiny print; you won’t have time to get a magnifier out during an emergency, so read the labels before use.
A good practice is for job planners to include the label information for each applicable chemical in each job package or work order.
Material Data Sheets
The MDS provides valuable safety information, covering such things as the recommended PPE, safe use and storage, and what to do in the event of inhalation or skin contact.
Another thing the label does is name the material and who makes it. You can easily use this to find more information online. You can, for example, find the latest MDS instead of relying on a paper copy that shipped with the product months ago. Why bother doing this? Because the MDS gets updated as new information comes in from various sources, including user incident reports.
Employee Training
Does your employer have a “check the box” HCS training program? To answer that, think about how well this program helps you learn about the chemicals you use on the job and how to protect yourself from harm. For example, are you learning about correct spill containment and emergency medical actions?
If you are not getting what you need, the training program violates the intent of the HCS law and leaves you at risk. Tactfully bring this up to management and ask for a response.
Written Program
OSHA requires your employer to describe and explain its HCS system in writing. Have you read the HCS information? Is any chemical you’re using left out?
Suppose you discover outdated information in your employer’s HCS documentation. That means you also found a deficiency in your employer’s process for keeping the HCS documentation current. It should be easy for management to fix both issues, but they must be made aware of them.
The FACTOR System
OSHA recognizes four major classes of chemical hazard. Someone clever at OSHA came up with a way to remember these: FACTOR. It’s an acronym for Flammable and Corrosive Toxic or Reactive.
You can ignore the “and” and the “or” and just remember the list: flammable, corrosive, toxic, reactive. The FACTOR system provides instructions on handling and storage for each of these chemical classes.
A chemical can fall into more than one class. For example, it can be flammable, corrosive, and toxic; that combination isn’t uncommon.
Obviously, flammable chemicals burn, corrosive ones corrode, and toxic ones make you sick. Less obvious is what a reactive chemical is. That’s one that is at its nastiest when it combines with a specific other material. It’s the reaction of these two that is so dangerous, rather than either by itself (though each may also be dangerous by itself). Some chemicals have a long list of reactive pairs, so read the MDS carefully to identify any you need to keep separate.
Spills
Generally, you’re not expected to clean up spills. Your company’s HCS should specify the maximum size spill you might attempt to clean up; anything larger, and the risk to you (and probably others) is too great for that attempt. Your company should have a designated spill response team that has specialized training and specialized equipment.
Your main job in the event of a spill is to leave the area, and report the spill immediately. Warn others on your way out, and ensure both your supervisor and the spill response team are informed about the nature and location of the spill.
To prevent creating spills yourself — and to minimize them if they do occur — observe three practices:
1. Take only as much solvent (or whatever the chemical is) as you need. Use a small “working” container with a lid, and affix the lid when you’re not using the chemical.
2. Set the container on a flat surface (where it’s unlikely to get knocked over), or hold it with one hand while in use.
3. Focus on the job; distraction just about ensures you’ll spill.
HCS Success
Familiarity tends to breed complacency. The more you use a given chemical, the less likely you’ll be vigilant about protecting against its dangers. And that can end badly. Not only would this defeat your company’s HCS program, it could leave you seriously injured — or worse.
To prevent complacency (or simply forgetting the particulars), make a point of periodically discussing the MDS for a chemical you use with your coworkers who are also using that chemical. Or ask your supervisor to host a short safety meeting to do the same.
Lamendola is an electrical consultant located in Merriam, Kan. He can be reached at [email protected].
Sidebar: Harmonization
The HazCom section of OSHA’s website says, “…the Hazard Communication Standard (HCS) is now aligned with the Globally Harmonized System of Classification and Labeling of Chemicals (GHS). This update to the Hazard Communication Standard (HCS) will provide a common and coherent approach to classifying chemicals and communicating hazard information on labels and safety data sheets.”
About the Author
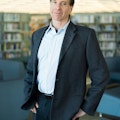
Mark Lamendola
Mark is an expert in maintenance management, having racked up an impressive track record during his time working in the field. He also has extensive knowledge of, and practical expertise with, the National Electrical Code (NEC). Through his consulting business, he provides articles and training materials on electrical topics, specializing in making difficult subjects easy to understand and focusing on the practical aspects of electrical work.
Prior to starting his own business, Mark served as the Technical Editor on EC&M for six years, worked three years in nuclear maintenance, six years as a contract project engineer/project manager, three years as a systems engineer, and three years in plant maintenance management.
Mark earned an AAS degree from Rock Valley College, a BSEET from Columbia Pacific University, and an MBA from Lake Erie College. He’s also completed several related certifications over the years and even was formerly licensed as a Master Electrician. He is a Senior Member of the IEEE and past Chairman of the Kansas City Chapters of both the IEEE and the IEEE Computer Society. Mark also served as the program director for, a board member of, and webmaster of, the Midwest Chapter of the 7x24 Exchange. He has also held memberships with the following organizations: NETA, NFPA, International Association of Webmasters, and Institute of Certified Professional Managers.