In Art. 110 of NFPA 70E, Standard for Electrical Safety in the Workplace, you’ll find a list of requirements for an electrical safety program [110.1(A)-(I)]. Near the end of this list is a paragraph addressing the job briefing [110.1(H)]. Figure 1.1 of Informative Annex I provides a “sample job briefing and planning checklist.”
Who conducts this briefing, and who must participate in it? NFPA 70E says “the employee in charge” conducts the briefing with “the employees involved.” So who is the employee in charge?
Typically, it’s the foreman or crew leader. Why wouldn’t it be the project manager? It could be, if the project manager is conducting a job-specific briefing with the crew that will specifically work that job.
The briefing is not a project-level thing — it’s a job-specific thing. The hazards, energy sources, and many other considerations will vary from job to job. The crew that’s replacing a motor has different safety and work process considerations than does a nearby crew installing controls in a panel. They might be working on the same project, but each is working a different job.
What it covers.
The person conducting the job briefing may need considerable time to prepare for that briefing, because it must cover the following:
• Hazards associated with the job. This means all potential hazards, not just electrical ones. These include mechanical energy sources, chemicals, falling hazards, and egress issues. It can also mean hazards that were not present when the risk assessment was performed. For example, a large item of production equipment must undergo unscheduled repairs. Thus, there’s more clutter and foot traffic, and welding is anticipated.
• Work procedures involved. This information area could easily be glossed over. An organization that values the consistency, efficiency, and quality of work already has a library of written procedures. If your organization doesn’t have written procedures, it’s at a competitive disadvantage and a safety disadvantage. Identify which procedures are applicable to the work. If there’s something critical to highlight, then do so.
• Special precautions. Article 110 doesn’t differentiate a “special” precaution from one that’s not special, at least not with definitions of either. A good indication of the meaning, however, is found in “work procedures involved.” Is a precaution wise in this circumstance but not identified in the applicable work procedures? Extra precaution could be for anything the crew might not observe, think of, or have reason to otherwise be aware of. Or something that isn’t normal; for example, today lift trucks will be driving past the switchgear area due to an equipment move.
• Energy source controls. You may notice this doesn’t say “breaker or fuse.” It doesn’t say “power source” or “circuit supply” or “disconnecting device.” It means all energy sources, including kinetic, hydraulic, pneumatic, and mechanical. To control kinetic energy, you might use wooden blocks or metal chains. To control hydraulic or pneumatic sources, you might use shut-off valves. And for a mechanical source, such as a spring, you might have a mechanic unload the spring tension.
• PPE requirements. This information should come from two places: the risk assessment (see Informational Annex F) and a survey of the work location prior to the briefing. Maybe the risk assessment was performed when the big stamping press wasn’t running. But today it is. Will the hearing protection indicated in the risk assessment be sufficient?
• Work permit. If you’re working on an energized electrical work permit, cover the information contained in the permit. You’ll find a sample electrical work permit in Informative Annex J, along with a flow chart for using it. Covering the work permit requires more than a few minutes. Don’t try to save time by glossing over it. Take the time to ensure everyone understands what the permit contains and what each person’s responsibilities are.
And if something changes during the course of the work, the person responsible for the job briefing has to update the involved employees of anything that might affect their safety. For example, they are working on a confined entry permit, and now another crew is entering the same confined space. How does this affect extraction, attendant duties, lockout/tagout, and just accommodating each other? Will that crew introduce a new hazard the crew hasn’t prepared for?
Dissecting the job briefing and planning checklist.
Informative Annex I provides a sample job briefing and planning checklist that consists of six sections (Checklist):
1. Identify.
2. Ask.
3. Check.
4. Know.
5. Think.
6. Prepare for an emergency.
These are arranged in the typical order of the work flow. Handling the first two sections is primarily the job of the job planner. As the work flow progresses through the check list, the person conducting the briefing has more responsibility.
The “Identify” section has 10 items to address. These include the number of people required to do the job, skills required, and available incident energy. Some of this information will need to be communicated during the briefing, some will not.
The Ask section provides three questions:
1. Can the equipment be de-energized?
2. Are backfeeds possible?
3. Is a standby person required?
As with the “Identify” items, these questions must be asked by the job planner. The person conducting the briefing should ensure they’ve also been answered.
The Check section contains seven items, including job plans, safety procedures, and vendor information. But one item (“Individuals are familiar with the facility”) involves communicating with the crew to ensure each person actually is familiar with the facility. If yours is a maintenance operation, this task typically belongs in “new hire” training. If your organization performs contract work on a location that is new to any crew member, this must be addressed as part of the briefing.
The Know section has three requirements. The person conducting the briefing needs to know:
1. What the job is.
2. Who else needs to know what the job is (and tell them).
3. Who’s in charge. In this context, don’t limit your thinking to the “employee in charge” referred to earlier.
Often, more than one person is “in charge.” Maybe several, each having a different area of responsibility.
If yours is a maintenance organization, both the maintenance supervisor and the production supervisor may be in charge. Typically the maintenance supervisor is in charge of the job, but the production supervisor is in charge of the equipment and/or the location. A safety administrator may be in charge of permitting activities to proceed. If a confined entry permit is involved, another person may be in charge of the confined space. And security people….
Let’s say yours is an electrical contracting firm, and the job is at a client’s location. You’ll likely have the same people in charge as the maintenance organization does. Ideally, those people will work through your “single point of contact.”
You also must know who is not in charge. What if you’re in the middle of a job and an employee of the customer firm starts giving verbal instructions? Is the customer always right? Not exactly. Unless it’s something urgent (e.g., safety problem), you don’t just follow those instructions. If you have a single point of contact, refer the question to that person. Depending upon the issue, you may need to stop work (or that particular task) until resolution is reached.
The Think section contains seven items, with the last one being “What else?” These items are good to discuss with the person(s) in charge, not just the crew.
The last section is important to cover during the briefing, as it’s about emergency preparation. One of its 10 questions: “Is the required emergency equipment available?” This (and most other questions here) should also be answered by each crew member.
Suppose the job is in a process plant, and you’ll be working in an area that requires an emergency eyewash station. When you enter the area, locate that eyewash and fix in your mind exactly where it is. If it’s a piped eyewash, test it; and be sure to flush it (run for a bit) to ensure the water is clean. If it’s a portable eyewash, check that the bottles are full, and you understand how to operate it. Any problems? Leave the area until they are resolved.
Another question is whether confined space rescue is available. If the use of extraction gear could become necessary, then rescue is not actually available unless that gear is actually worn by the person(s) entering the confined space and a qualified attendant is standing by.
Not so fast
Even though we’ve referred to only one paragraph and a checklist, you can see that a good job briefing is not a quick “check off the box” exercise. It requires preparation, organization, and communication. If you put good effort into the briefing, both it and your job should go smoothly.
Lamendola is an electrical consultant located in Merriam, Kan. He can be reached at [email protected].
About the Author
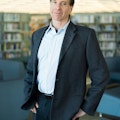
Mark Lamendola
Mark is an expert in maintenance management, having racked up an impressive track record during his time working in the field. He also has extensive knowledge of, and practical expertise with, the National Electrical Code (NEC). Through his consulting business, he provides articles and training materials on electrical topics, specializing in making difficult subjects easy to understand and focusing on the practical aspects of electrical work.
Prior to starting his own business, Mark served as the Technical Editor on EC&M for six years, worked three years in nuclear maintenance, six years as a contract project engineer/project manager, three years as a systems engineer, and three years in plant maintenance management.
Mark earned an AAS degree from Rock Valley College, a BSEET from Columbia Pacific University, and an MBA from Lake Erie College. He’s also completed several related certifications over the years and even was formerly licensed as a Master Electrician. He is a Senior Member of the IEEE and past Chairman of the Kansas City Chapters of both the IEEE and the IEEE Computer Society. Mark also served as the program director for, a board member of, and webmaster of, the Midwest Chapter of the 7x24 Exchange. He has also held memberships with the following organizations: NETA, NFPA, International Association of Webmasters, and Institute of Certified Professional Managers.