Let’s say you work for an electrical services company that performs industrial maintenance. Your company recently landed a new client that has decided to outsource all of the electrical maintenance other than direct support to production. Your boss told you they made this decision due to problems retaining enough skilled maintenance personnel. So the ones they still have will respond to equipment failures. Your company will provide the predictive and preventive maintenance needed to reduce those failures. You are the onsite supervisor for your company’s crew.
This is steady work and it’s in town, so keeping this customer is important. But after a week of working there, you understand why they had problems keeping qualified people. In looking over their maintenance practices, you can see they were insufficient. For example, there has never been a cable testing program, there’s no record of any breaker maintenance, and a power quality analysis has never been done. In short, the plant has been in reaction mode for years.
This situation resulted in an excessively high failure rate, which adversely affected the plant’s ability to meet its production obligations. During the past week, you’ve observed the effects of this on safety.
Production managers push the repair technicians to cut corners. They are actually told not to “waste time” locking out disconnects. When they are trying to work, production managers hover over them and tell them to hurry. The general attitude is that safety gets in the way. Even your own people have been chided for “wasting time” and “setting a bad example.”
While the pressure is understandable, this way of coping with it is not acceptable. How can you communicate this to the customer without offending them?
First, understand that you are not going to get these production managers to change their behavior. You need someone else to do that. Start with the plant manager. Ask for a private meeting. Start the meeting by saying that uptime and profitability are important. At this point, you could position safety as being “also important” or “more important” but that is going to be a hard sell under these conditions.
Instead, explain that you have ways of removing inefficiency from both your work and the work being done by the inhouse maintenance staff thus reducing equipment downtime and repair costs dramatically. That will get the plant manager’s eager attention. If the plant manager doesn’t ask, “How can I help,” tell the plant manger, “Here’s how you can help.”
In a nutshell, the production managers must stop undermining safe and effective work practices with their badgering and interference. They mean well, but they are exacerbating the very problems they are trying to solve. When the plant manager agrees to this, you then say you’ll submit a daily report for a while to ensure compliance; this step makes him accountable for holding his people accountable. And he’s going to want to do that to make his production numbers so he can keep his job.
About the Author
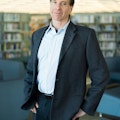
Mark Lamendola
Mark is an expert in maintenance management, having racked up an impressive track record during his time working in the field. He also has extensive knowledge of, and practical expertise with, the National Electrical Code (NEC). Through his consulting business, he provides articles and training materials on electrical topics, specializing in making difficult subjects easy to understand and focusing on the practical aspects of electrical work.
Prior to starting his own business, Mark served as the Technical Editor on EC&M for six years, worked three years in nuclear maintenance, six years as a contract project engineer/project manager, three years as a systems engineer, and three years in plant maintenance management.
Mark earned an AAS degree from Rock Valley College, a BSEET from Columbia Pacific University, and an MBA from Lake Erie College. He’s also completed several related certifications over the years and even was formerly licensed as a Master Electrician. He is a Senior Member of the IEEE and past Chairman of the Kansas City Chapters of both the IEEE and the IEEE Computer Society. Mark also served as the program director for, a board member of, and webmaster of, the Midwest Chapter of the 7x24 Exchange. He has also held memberships with the following organizations: NETA, NFPA, International Association of Webmasters, and Institute of Certified Professional Managers.