So you just spent three hours removing and replacing a motor that drives the feed to a robotic welder. You connected the leads exactly the way they were before you disconnected them. You properly closed the motor weatherhead and correctly reconnected the motor coupling to the load.
You then took your lock off the disconnect, closed it, and told the operator to go ahead and start the machine. Oops — the motor ran backwards and kinked the metal sheet bank into the feed roll, a problem that will take “only” another hour to fix.
What step did you leave out, and how should you have performed it? The missing step was motor rotation testing. In a moment, we’ll answer the second half of that question.
If you connect a motor to its load without first testing the rotational direction, you can damage the load. The type of damage, of course, depends upon the type of load. But even if reversal won’t cause damage to the load, it can cause confusion. For example, the operator’s direction indication will be backwards. Or consider the case of a motor-driven impeller in a mixer; probably no damage, but if the impeller is directional in its design, you will get inadequate mixing and many ruined batches.
Regardless of the application, it’s a good practice to always test rotation. If a 3-phase motor rotates in the wrong direction, you can swap any two leads to change to the desired direction.
One way to test motor direction is to take your best guess on how to connect the leads, then run the motor and note the direction it spins. If you’re wrong, you undo two leads and swap the wires. Just to make sure, run the motor again. If it spins in the correct direction, you can then couple it to the load.
This approach is time-consuming, especially if you must do this testing with the motor not mounted or installed, and consequently have to rig up extensions for those supply leads. For example, if you’re working with a C-Face motor, the coupling and mounting are typically the same thing. In many hermetic motor applications, a similar dynamic is at work.
A better way is to use a phase rotation meter. Let’s assume the meter you’re using is designed for 3-phase motors, and you are installing a 3-phase motor. Your meter has six leads on it, three on the load (or motor) side and three on the supply (or line) side.
There are two steps. First determine which leads on the motor are A, B, and C phase; then determine which leads on the supply correspond. You don’t have to connect the motor to the supply during this process.
This meter enables you to turn the shaft of the motor by hand, and observe an indication on the meter as to whether the motor connections are correct. Suppose the shaft needs to turn counterclockwise during normal operation. You connect the three load (or motor) leads to the motor terminals, then spin the shaft counterclockwise. If the meter tells you the connection is incorrect, you swap any two leads and try again. Once the meter indicates you’ve got this right, you then label the leads of the motor to match the A, B, and C leads of the tester.
But you’re not finished just yet. What remains is to correctly mark the supply, so you can match the two. Now you’ll use the other side of the meter. Isolate the power (de-energize) before connecting the meter to the supply leads (i.e., open the disconnect). After you’ve made the connections, energize the supply and see what the meter says. If the meter says the connection is wrong, isolate the power again, and swap any two leads. Once the meter shows you have the correct connections, isolate the power again, and connect the motor A, B, and C leads to the corresponding A, B, and C supply leads.
If you make it your standard practice to always perform this testing before connecting a motor to its supply, you will have zero risk of damaging something because you mistakenly thought the direction didn’t matter in this application. Yes, it will take a little more time on those applications where direction doesn’t matter. However, think of all the time it will save versus the one time you thought it didn’t matter, but it did.
Testing beats guessing, every time.
About the Author
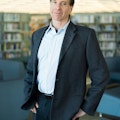
Mark Lamendola
Mark is an expert in maintenance management, having racked up an impressive track record during his time working in the field. He also has extensive knowledge of, and practical expertise with, the National Electrical Code (NEC). Through his consulting business, he provides articles and training materials on electrical topics, specializing in making difficult subjects easy to understand and focusing on the practical aspects of electrical work.
Prior to starting his own business, Mark served as the Technical Editor on EC&M for six years, worked three years in nuclear maintenance, six years as a contract project engineer/project manager, three years as a systems engineer, and three years in plant maintenance management.
Mark earned an AAS degree from Rock Valley College, a BSEET from Columbia Pacific University, and an MBA from Lake Erie College. He’s also completed several related certifications over the years and even was formerly licensed as a Master Electrician. He is a Senior Member of the IEEE and past Chairman of the Kansas City Chapters of both the IEEE and the IEEE Computer Society. Mark also served as the program director for, a board member of, and webmaster of, the Midwest Chapter of the 7x24 Exchange. He has also held memberships with the following organizations: NETA, NFPA, International Association of Webmasters, and Institute of Certified Professional Managers.