LED lighting has received massive attention in the past couple of years, and rightfully so. The right LED system for the application will improve lighting and save energy. But there’s a significant investment upfront. And the project can under-deliver relative to expectations because the technology choice alone doesn’t solve all lighting problems and energy waste problems.
Before you go ahead with that big project, take a closer look at your existing lighting and its environment. Here are some typical problems that, if solved, can reduce the reliance on “tacked on” task lighting or forestall an expensive replacement project by providing more useful light with less energy use:
- Overhead luminaire in the wrong location relative to work surface or lamp mis-aimed. Move the work surface or move (or re-aim) the luminaire.
- Obstacles blocking light and creating shadows. Similar to the previous problem, but what if the obstacle can’t be moved? You may be able to replace the existing lamp with a much lower lumen (and wattage) version; this will reduce the shadows while saving energy. If the work surface doesn’t have enough light after this, add task lighting; you may have a net gain in usable lumens and net reduction in energy usage.
- Dirty lenses. This is a common malady. The typical “solution” is to add task lighting. Instead, try cleaning the lenses; people will think you installed new lights.
- Maladjusted shades. Many luminaires have adjustable shades. Try different shade settings.
Here are some low-cost energy savings measures:
- Replace magnetic ballasts. This alone justifies an upgrade, but not necessarily to a whole new system. If you can upgrade just the ballast (you might have to also upgrade the lamp), the cost savings will be considerable. For example, you have a warehouse with High Intensity Discharge (HID) luminaires. Replacing the magnetic HID ballasts with eHID ones may be the way to go. Look into it.
- Add controls. Automatic dimmers, daylight controls, and occupancy controls can produce significant energy savings even if you add more of the same type of lighting.
- Correct for voltage drop, if you have long runs. You don’t need to upsize all of the conductors to see significant improvement; you might make do with just upsizing your “back bone” conductors.
- Identify and correct power quality problems. Low power factor (PF), in particular, should be high on your list of items to address. If your existing ballasts don’t have PF correction, contact the manufacturer about a possible fix for the existing ballasts.
About the Author
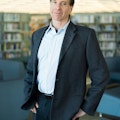
Mark Lamendola
Mark is an expert in maintenance management, having racked up an impressive track record during his time working in the field. He also has extensive knowledge of, and practical expertise with, the National Electrical Code (NEC). Through his consulting business, he provides articles and training materials on electrical topics, specializing in making difficult subjects easy to understand and focusing on the practical aspects of electrical work.
Prior to starting his own business, Mark served as the Technical Editor on EC&M for six years, worked three years in nuclear maintenance, six years as a contract project engineer/project manager, three years as a systems engineer, and three years in plant maintenance management.
Mark earned an AAS degree from Rock Valley College, a BSEET from Columbia Pacific University, and an MBA from Lake Erie College. He’s also completed several related certifications over the years and even was formerly licensed as a Master Electrician. He is a Senior Member of the IEEE and past Chairman of the Kansas City Chapters of both the IEEE and the IEEE Computer Society. Mark also served as the program director for, a board member of, and webmaster of, the Midwest Chapter of the 7x24 Exchange. He has also held memberships with the following organizations: NETA, NFPA, International Association of Webmasters, and Institute of Certified Professional Managers.